Energy-efficient ultrasonic welding in the smallest spaces
Welding Conductor Cross-Sections from 10 to 95 mm² to Terminals.
Driven by the rise of electromobility and energy technologies, the demand for terminal welding systems is growing rapidly. Ultrasonic systems are often the ideal solution, as they produce highly robust connections without compromising conductivity—all within short cycle times. However, application requirements are becoming increasingly diverse. Compact solutions are in demand—systems that minimize expensive floor space usage, are tailored precisely to the task at hand, and can be easily adapted to future needs.
Terminal welding involves joining cables to contact elements (known as terminals), for both high-voltage and low-voltage applications. High-voltage applications in particular place stringent demands on contact quality. In the automotive industry, for example, such connections must remain reliable for years under harsh conditions such as vibration and temperature fluctuations. In these cases, ultrasonic welding has proven its value. The process is fast, gentle on materials, and requires little energy. It also allows continuous monitoring and documentation of all relevant process parameters during welding, ensuring high quality.
For applications involving smaller conductor cross-sections from 10 to 95 mm², Telsonic has expanded its portfolio. Beginning in spring 2025, the company will offer the compact TelsoTerminal TT6 in performance classes of 7.2 kW and 9.6 kW.
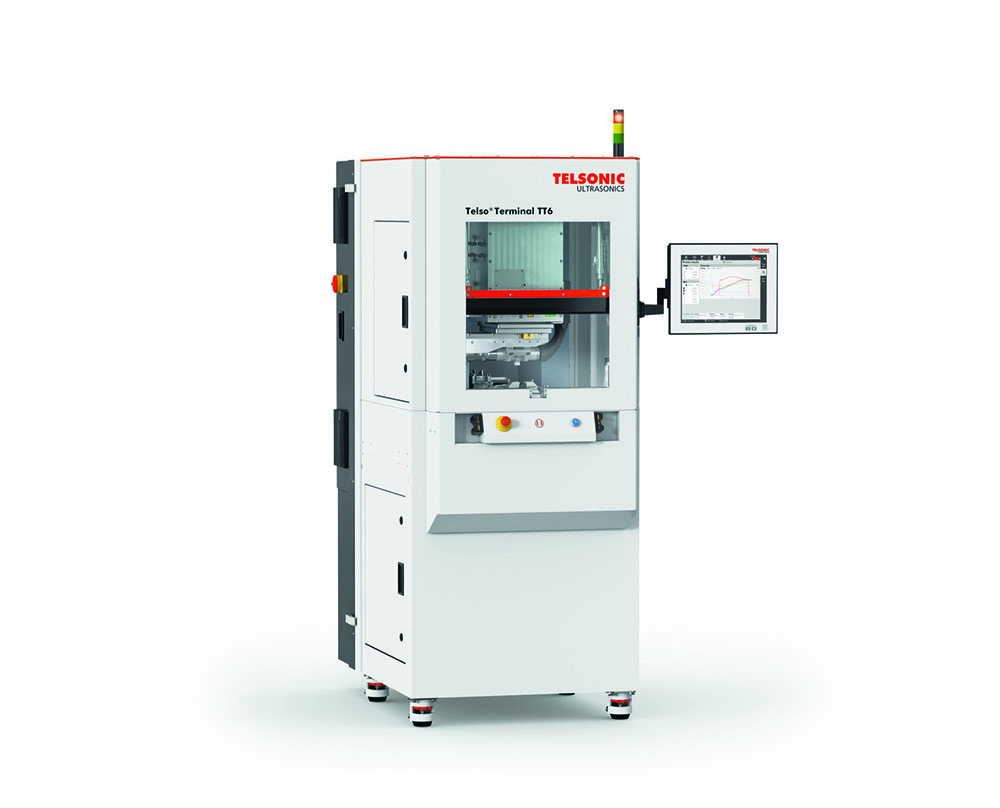
Flexibility in Minimal Space
This ultrasonic metal welding system is specifically designed for welding cables to terminals or short terminal-to-terminal connections. It uses the same welding process as its “big brother,” the TelsoTerminal TT7, along with the same clamping system and tools. This simplifies application transfers between machines. However, the new system loads cables and terminals from the front, and its compact design saves valuable production space.
The machine is operated via an optimized user interface with a 15-inch touchscreen. The generators are specially configured for applications requiring lower welding power. Standard welding capacity ranges from 10 to 70 mm² for the 7.2 kW version and from 16 to 95 mm² for the 9.6 kW version. Welding a 95 mm² copper cable to a terminal, including cooling time, takes just 15 seconds.
Thanks to the wide adjustment range of the ultrasonic generators, these systems can be quickly adapted to various applications with different cross-sections, with no significant retooling effort. Only the tooling needs to be changed—a task that takes less than five minutes. Unlike many market-standard solutions, no generator upgrades or expensive extra components are required. This flexibility ensures long-term investment security. Users also benefit from low energy consumption, high process reliability, easy integration via OPC UA, and long tool life.
Torsional Welding Process for Superior Connections
Telsonic’s patented PowerWheel® welding technology ensures high contact quality. Welding is performed using a rocking, rolling motion directly over the joining area. This ensures maximum amplitude is focused in the center of the weld zone, delivering power precisely where needed. Compared to linear systems, welds can be up to 30% narrower—offering significant material and space savings.
Another advantage is the ability to produce narrow but thick weld nodes with high strength, significantly reducing the risk of cable breakage compared to linear systems. Telsonic’s standardized PowerWheel sonotrodes are optimized for both copper and aluminum. They meet OEM and wire harness manufacturer specifications and comply with USCAR 38 (performance specification for ultrasonic welded wire terminations). As with conventional ultrasonic welding, the system is suitable for all non-ferrous metals.
Maximum Quality via Real-Time Measurement and Digital Process Control
The torsional motion is not the only contributor to weld quality. The direct vertical force applied to the weld area is also critical. While many systems measure only pneumatic pressure, weld time, and delivered energy, Telsonic’s solution uses an integrated load cell to measure the actual force applied to the weld. This enables highly precise detection of deviations during production.
Transparency and flexibility are key: applied force is measured in Newtons—not pneumatic pressure—making the system independent of the pneumatic environment and easier to adapt to other machines. The same goes for weld amplitude, which is displayed as an absolute value in micrometers (µm), rather than as a percentage, as is common in the industry.
Optionally, the system can also monitor the converter temperature to protect it from overload. Additional sensors can measure the diameter of inserted cables and the height of the terminals to ensure the correct parts are used and correctly positioned. This reduces the risk of expensive material waste before welding begins. All data is logged and linked to the specific welding process.
Digitalization Enables Optimal Results
Ideally, process and quality data should not be confined to individual machines but integrated into higher-level plant control systems. To that end, the TT6 features an OPC UA interface for standardized, simple communication with existing production control systems or MES platforms. A Java-based MES Connector SDK is also optionally available, allowing operators to integrate the machine into their MES environment quickly, easily, and independently. This enables flexible, vendor-independent access to all relevant process and product data—for both process optimization and quality assurance.
Telsonic systems leverage many advantages of digitalization. Even changeovers between production orders benefit. For example, digital checklists help avoid errors during tool changes. Once a new job is loaded, the system guides the operator step by step through the retooling process. Barcodes on the tool documentation can be scanned to verify the correct sonotrode is installed. The checklist ensures all steps are completed correctly before resuming production.
The technological advantages of this new terminal welding system are diverse. With its cost-efficient and environmentally friendly ultrasonic welding process, the TT6 opens up new application areas where high reliability and minimal space requirements are essential.
Learn more at telsonic.com
About Telsonic
The Swiss Telsonic Group has been delivering industrial ultrasonic solutions across Europe, the Americas, and Asia since 1966. Continuous innovation has enabled Telsonic to develop a competitive edge in many applications, offering real added value to its customers. With more than 300 highly qualified employees, this owner-managed company specializes in ultrasonic welding of plastics and metals, as well as ultrasonic cleaning and sieving. Customers around the world—especially in the automotive, packaging, and medical technology industries—appreciate Telsonic’s broad range of ultrasonic components for machine builders and its complete welding systems.
Source link